Can an Air Compressor Explode? 6 Causes & Fixes
TheToolGeeks.com is a participant in the Amazon Services LLC Associates Program and other affiliate advertising programs. We may earn from qualifying purchases. (Learn More).
There are several videos around the internet showing the explosion of air compressors. And we’ve been asked several times, can an air compressor explode?
While it is technically possible, as it’s an electrical tool with a pressurized air tank, it is UNLIKELY to happen. Most air compressors are perfectly safe, especially if you follow the instructions when using one and perform the recommended maintenance.
But there are a few things that you should know if you’re concerned about your air compressor exploding and to prevent that from ever happening. In this article, we’ll highlight all the key things that every air compressor user should know.
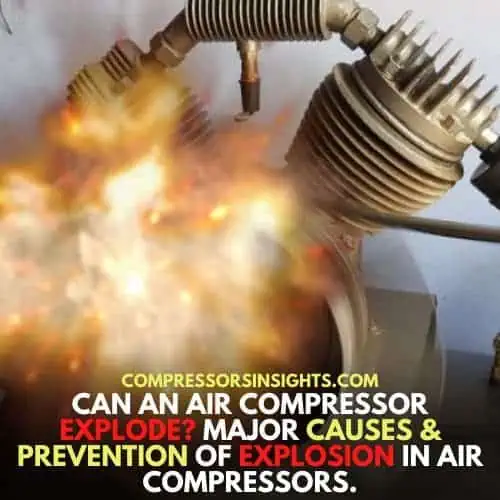
Can an Air Compressor Explode?
An air compressor works by taking in air and compressing it to a higher pressure, which is then stored in a tank (usually rated in gallons). To help you understand the working principle of air compressors, we’ll split the operation of an air compressor into steps:
Intake – The compressor draws in air through an intake valve, usually located on the side or top of the compressor.
Air compression (pressurized air) – The air is then compressed by reducing its volume, which increases its pressure. The compressed air is stored in a tank or reservoir.
Air discharge – The compressed air is then delivered through a hose or piping system to power pneumatic tools or other equipment.
You see, in the operation of an air compressor, the air pressurization, storage, and discharge of pressurized air are involved, which is why an air compressor could be vulnerable to an explosion (under certain circumstances). But what are those circumstances?
What are the reasons for Air Compressor Explosions?
An air compressor exploding might be the rarest occurring issue. Again, it usually does NOT happen. But the following reasons could make it possible:
- The compressor is improperly handled
- Lack of proper maintenance
- The compressor is not assembled correctly
- Any part of the compressor come with or has a loose fitting
- The compressor tank has corrosion, which leads to the weakening of the tank structure
- Loose wiring, a damaged hose, or electricity issue
Let’s see how you can prevent and fix those issues while maintaining your air compressor and saving yourself from injury.
1. Leakage
Air compressors are machines that need to be taken care of, and sometimes leakage happens in the compressor tank when it is too old. Besides the tanks, the valves or drainage plug leakage can cause an explosion.
How to fix the leakage?
We recommend changing the old compressor tank or the entire compressor.
If the issue is the valve or drainage plug, you should replace the valves or plug (we discuss further in the article).
Although you can fix the leakage with welding, we don’t recommend this option. Welding the compressor tank should be avoided, as this type of resolution could cause another leak or explosion after some time.
2. Corrosion
The corrosion inside the compressor happens primarily due to moisture accumulation inside the tank. Moisture naturally accumulates due to the air pressurization. This is why keeping the compressor dry and clean when not in use is recommended. Compressor corrosion can be the most significant reason behind tank failures.
Sometimes, people do not drain the tank after using the compressor and let it sit. Even if you drain the tank, let it stay open to dry out properly before closing it.
If you notice any rusty air coming out of your air compressor, then it’s time to get rid of the rust.
How to get rid of rust in an air compressor?
You can use vinegar at home to clean out the compressor tank. Just fill the water inside the tank and drain it. Next, fill the compressor with vinegar, and if you have time, let it stay overnight or add a small amount of another acid to properly clean it.
Besides vinegar, there are market-based chemicals that you can use to clean the tank properly, but only use those chemicals for a short period of time to avoid corrosion of the tank walls.
3. Faulty Safety Valve and Automatic Pressure Switch
The function of the compressor safety valve is to keep pressure in the system below the maximum pressure rating of the compressor. That means the safety valve’s work is simple but crucial as it protects the unit from exceeding the pressure limit by releasing pressure once it hits the rating limit.
On the other hand, the automatic pressure switch is more precise, as it switches off the compressor if it exceeds the pre-set pressure level.
Think about what would happen if one or both are not working correctly. The pressure in the compressor system will exceed its limit and put the compressor in danger of exploding. Therefore, checking if the safety valve and automatic pressure switch are working correctly is critical. If not, you should replace them. You can easily test your valve and switch to determine if they release pressure and shut off the air compressor after reaching the pre-set pressure limits.
How to replace the safety valve?
The only solution to this problem is replacing it with another safety valve.
- Before anything drains, your compressor should be shut off.
- Then remove the gauge shroud, and you will have access to the safety valve.
- Using a socket wrench, remove the safety valve from the manifold (rings should be removed before).
- Then, replace it with a new valve, and you are ready.
Replacing the pressure switch:
- Ensure the compressor is unplugged, and then remove the cap of the new and old pressure switches.
- Unplug all the wires from the previous switch ( green, black, and white wires). Remember the configuration. We take pictures of connections before disconnecting any assembly.
- Then, using a suitable wrench, remove the switch from the unit and replace it with a new one.
- And lastly, connect all the wires at the right position and cover the switch, and you are good to go.
4. Clogged Filters
We always recommend cleaning the air filters of an air compressor. It ensures the compressor gets clean air and removes dust particles.
When you don’t clean it, it clogs, and eventually, the air pressure will build up, and your air compressor could exceed its pressure limits and explode. Usually, if the air filter of your air compressor is clogged, you will notice a change in the sound of your air compressor, or its noise will unexpectedly increase.
How to replace the filter?
- Simply unscrew the bolt from the filter cover and then remove it.
- Next, remove the old and clogged filters from the unit and clean or replace them. (mostly should be replaced instead of cleaned).
- And then, cover the compressor and tighten the bolt again.
5. Faulty Pressure Relief valve
The purpose of a pressure relief valve is to vent out the fluid through an overly pressurized vessel. This pre-set pressure valve ensures you have presented the pressure level and won’t let the compressor pressure buildup above it.
If the pressure relief valve malfunctions, your air compressor will exceed its pressure limit sooner or later, and that could spell trouble. Check if your pressure relief valve is working. If not, then you should replace it with a new one.
How to replace the pressure relief valve?
- Unscrew the bolt holding the valve in place
- Then, use a wrench to remove the relief valve.
- Put the new valve in place and screw the bolt back in to hold the valve properly.
6. Faulty Thermal Overload Protector
It protects the whole compressor or the motor from any damage in case of electricity disturbance or if it becomes overheated. How? It turns off the electricity, which helps prevent the motor from heat damage or fire (it is attached to the motor, or in some air compressors, it’s inside it).
You can test your overload protector with a multimeter (continuity test). Simply attach the probes of the multimeter to both terminals of the overload protector, and set your multimeter knob at the diode symbol (or sound wave symbol in some multimeters). Your overload protector is fine if your multimeter shows values or gives a beep sound. Otherwise, it’s faulty and should be replaced.
How to fix it:
- Unplug your air compressor from the power source.
- Check the user manual to find out the location of the thermal overload protector in your air compressor (usually, it’s enclosed in the cover).
- Unthread all screws of the cover and remove the cover.
- Detach overload relay.
- Once the relay is removed, pry off the old overload protector and detach its wire.
- Take the new compressor overload protector and attach its wire to the appropriate terminal.
- Align the new overload protector onto the compressor motor pins and push it into place.
- Realign the relay on the motor pins and push it back into place.
- Ensure that everything is securely in place before testing the compressor.
Note: If you’re not a technical person, do not do the replacement alone. Instead, hire someone who can do this correctly for you. Also, the steps mentioned above for replacing the components may vary depending on your air compressor brand and model.
These are some of the factors that may play a significant role in the explosion of your air compressor tank. Make sure to eliminate all these faults if you notice them in your air compressor.
How can you prevent an explosion in an air compressor?
To prevent your compressor from possible explosion, you need to manage it properly and maintain it. Follow these to keep your air compressor in good working order and prevent your compressor from explosion:
- The most important step is drainage: drain your compressor after using it, let it dry for some time, plug it, and then store it.
- You should always do a brief research on the compressor and then buy it. (never buy without researching).
- Oil-free compressors are the best choice if you do not want to spend time on maintenance, but if your compressor is oil-lubricated, check it and lubricate it on a regular basis.
- You should know how much and how long your compressor can work. Never abuse your compressor with a lot of working time.
- Avoid repairing continuously and instead replace it. Repaired compressor will break again and eventually will explode.
- The small parts, valves, fitting, etc., are crucial because it will be bad for the compressor if damaged. Keep a check on them.
- Using the exact pressure level compressor and how much you need is never recommended. Instead, buy a compressor that has more pressure. (you need 120 PSI to buy with a 130-150 PSI compressor).
- Pre-set the compressor according to your working requirements and your project needs.
- Avoid using compressors in closed rooms and use them in open areas instead. (ventilated areas).
- Keep a check on your compressor’s overall health by performing scheduled maintenance.
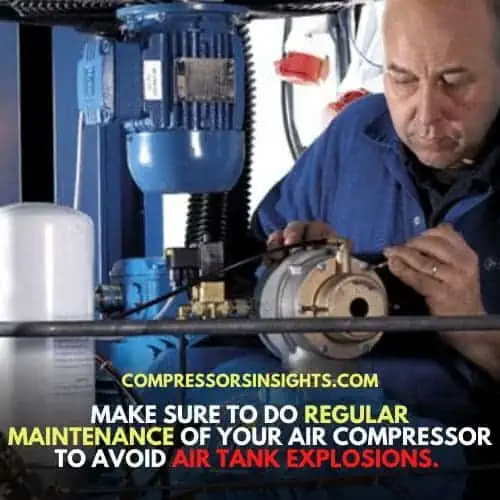
The Life Expectancy of Air Compressors
The life span of the compressor depends on the quality of the compressor and the maintenance performed. A high-quality compressor can easily last up to 8-10 years with proper care and maintenance.
Always go for high quality instead of the price. It will not last long if the quality is bad.
Additionally, avoid repairing your air compressor if it has exceeded its lifespan and opt to replace it instead.
What Happens When an air compressor explodes?
Storytime: Sometime back, there was an explosion during the daytime when the garage owner was about 25 feet away from the garage, and he heard and felt a blast-like explosion.
When he opened his garage, he saw that his air compressor had exploded. Thankfully he was not near the compressor or garage when it occurred.
What were the results of the explosion? The windows of the garage and the door behind the compressor were broken. Even the neighbors around 75 yards away could feel the explosion. Other tools in the garage were damaged pretty badly.
When he checked, the cause was due to rust buildup in the compressor, which was fully bursting and spreading throughout the garage. The rust build up was entirely preventable.
So be careful, operate the compressor according to its instructions, and keep the compressor cleaned and maintained.
FAQs
Can an air compressor explode if left on?
No, you can leave your compressor on for an entire day. It will not immediately affect the compressor, but the continuous pressure in the tank will weaken the seal and may result in eventual leakage.
Can an air compressor explode in heat?
Yes, when there is poor lubrication, it increases friction and leads the oil into the valves. The oil can cause an explosion. Poor lubrication can also cause overheating, leading to a compressor explosion.
Is it safe if I don’t drain my air compressor?
Draining the compressor regularly or after every use is recommended. Otherwise, it will cause rusting in the bottom of the compressor tank, which weakens the tank walls.
Amazon and the Amazon logo are trademarks of Amazon.com, Inc, or its affiliates.